Nowadays quite a few people who want to take care of metal objects of everyday use are looking for the ideal solution on how to do it in order not to damage these objects. Although this type of processing of everyday objects can be done by hand, laser cutting is becoming an increasingly popular solution. Due to the numerous advantages of using such a method in everyday life as well as in the economy, it is worth knowing what exactly laser cutting is and why it is worth opting for this solution.
What is laser cutting?
To understand exactly what laser cutting is and what it consists of, it is worth knowing first of all what the laser itself is. According to the current definition, a laser is nothing more than the amplification of visible light by means of forced emission of infrared radiation. In other words – photons – which form the basis of the light beam are set in motion by an electric current. This, in turn, causes these particles to start emitting their energy in the form of light in the form of a beam. It is this beam that is called a laser beam, laser beam or laser.
The laser itself is, in turn, composed of three basic elements, which include an external pumping system, an optical resonator and an excited active medium. It is through the use of the aforementioned elements that the emission of a laser beam is possible. This in turn makes it possible, for example, to cut various types of metal objects both used in everyday life and in various industries.
What does laser cutting of metal surfaces look like?
Laser cutting is such a convenient method of precise cutting of various types of metal surfaces, because it allows rapid cutting of any size and thickness of objects. The laser beam, falling on the selected surface at the right angle and with equal intensity, is able to precisely melt and vaporize that small piece of metal surface.
The laser cutting process itself is based on the fact that, using the above-mentioned components that make up the laser beam, it is possible to set up the equipment with an adequate intensity of laser beam incidence to the size, form and thickness of the metal surface. Then it is also possible to set the diameter of such a laser beam, which is usually no more than half a millimeter and allows you to cut through the structure of the entire material or surface. Then all you need to do is to start the device and direct the laser beam to the designated area, so that you can get the effect of an evenly cut surface without having to act with greater forces on the cut sheet.
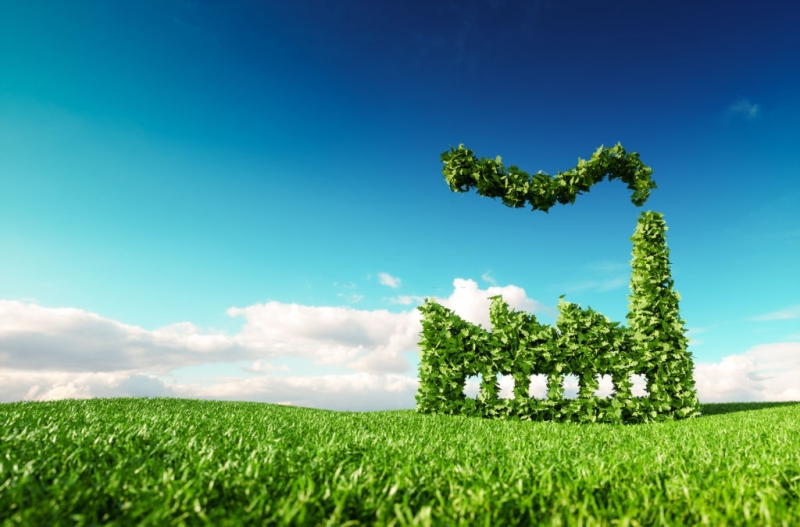
Advantages of using laser cutting in practice
Although some people may question the validity of using laser cutting in many situations, such a method undoubtedly has more advantages than traditional methods of cutting and reshaping selected surfaces. The advantages of laser cutting of metal surfaces undoubtedly include:
- theuniversal nature of the laser cutting process – laser cutting owes its universal nature primarily to the fact that by changing the intensity or volume of the laser beam, various modifications can be made to the selected metal surface. This can be understood as, for example, heating the selected metal surface by heat treatment, melting the selected part of the metal surface so that it can be shaped as desired, and vaporization. This makes it possible, for example, to clean a given surface from impurities located deeper in the metal structure, to engrave a selected surface or to increase resistance to external agents;
- ecological aspect – unlike traditional forms of metal cutting using, for example, more complicated equipment or force, laser cutting undoubtedly involves a positive aspect for the environment. We are talking here primarily about the fact that laser cutting provides a precisely executed change in the shape or thickness of a selected metal surface with virtually no production waste. In other words, laser cutting does not create unnecessary fragments of metal surfaces – and thus waste does not pollute the environment.
- financial aspect – another advantage that distinguishes laser cutting from other forms of metal surface alteration is the real possibility of saving money. Thanks to the fact that you can reduce (or completely eliminate) the costs associated with the processing or disposal of post-production waste, or reduce the costs associated with, for example, buying a similar metal object due to the lack of the possibility of changing its shape;
- thepossibility of arbitrary manipulation of the power and intensity of laser beams – thanks to the fact that you can freely adjust the power and intensity of laser beams to the selected surface, you can get amazing results. These would not be possible with other, for example, manual methods of modifying metal surfaces;
- lack of physical contact between thelaser cutting equipment and the surface being cut – another advantage of laser cutting is that during the process of cutting a metal surface there is virtually no physical contact between the laser beam generating equipment and the metal surface, such as sheet metal. This is extremely important, especially when you want to achieve the highest possible cleanliness around the metal surface being cut;
- elimination of cracks and minor mechanical damage with laser cutting – by using artificial shock waves and under the extremely high pressure generated by the laser beam, micro-cracks or minor dirt can be removed accurately in a simple way. This is very important especially for small surfaces such as cutlery.
Based on the above-mentioned advantages, it can be concluded that laser cutting is an ideal solution that can be used for all kinds of metal surface processing. It doesn’t matter what shape, thickness or form of metal surface the selected person wants to achieve – laser cutting, thanks to its precision, will be the best solution.
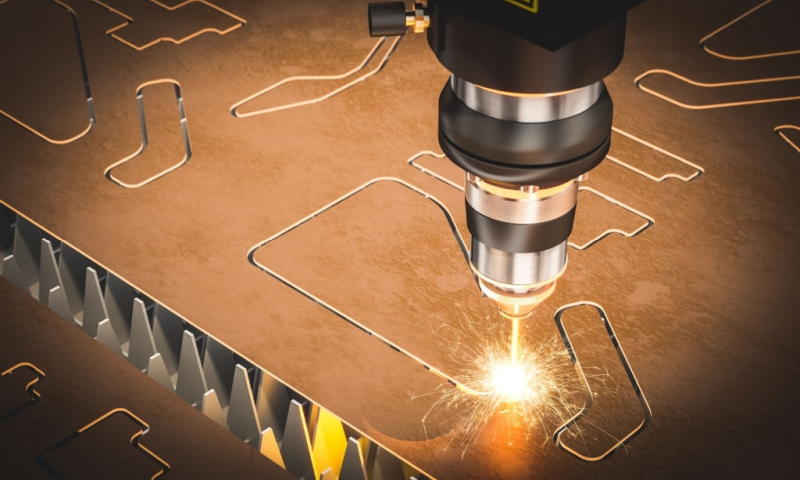
With what types of materials can laser cutting be used?
Contrary to what you might think, laser cutting can be used to form and cut through the prevailing metal and some other surfaces. Some of the most common examples of surfaces where laser cutting is used include:
- components for the automotive industry;
- domestic kitchen equipment, such as the manufacture of knives, forks, spoons and other kitchen equipment components;
- some components intended for military equipment;
- components used in electronics;
- small components used in mobile telephony;
- some metal components used in the aerospace industry.
In addition, laser cutting is used in the cutting of non-metallic surfaces such as ceramics, aluminum or stainless steel and nonferrous metals, among others.
Is it worth opting for laser cutting?
Based on the arguments presented above and the advantages regarding the use of laser cutting, it is safe to say that it is a solution that everyone can opt for. Due to the precision associated with this type of service, the preservation of surface cleanliness and a number of other advantages, it is the most economical and versatile method of changing the shape or form of selected metal and non-metal surfaces.